Comment fonctionne le système anaérobie (AIP) sur les sous-marins?
À la fin de la Seconde Guerre mondiale, l’ingénieur allemand Helmuth Walter a conçu le premier sous-marin avec la technologie AIP
Conception du S-80
Dans la réalisation de ce travail, il est destiné à répondre à la raison de l’installation d’un système indépendant de l’air , également connu sous le nom d’AIP pour son acronyme en anglais Air Independent Propulsion, pourquoi tant d’efforts dans son développement, expliquer son fonctionnement de base et avantages que ce nouveau système de propulsion apporterait à notre arme sous-marine, à la Marine et bien sûr à l’Espagne. Mais pour mieux comprendre l’intérêt de notre marine à équiper ses sous-marins de cette technologie, il faut remonter vingt ans en arrière. Après la construction de deux séries de sous-marins en consortium avec le DCNS français, les sous-marins des classes 60 et 70, la marine espagnole a estimé qu’un remplacement générationnel des anciens sous-marins de classe «Dolphin» et «Galerna» devait être envisagé. Pour cela,
après avoir défini les objectifs et les caractéristiques du sous-marin, en 2004, l’ordre d’exécution des 4 sous-marins, extensible à deux autres, a été signé et un an plus tard, NAVANTIA a commencé la construction du premier de la série.
Après la publication de divers problèmes de développement et d’un surpoids d’environ 75 tonnes supplémentaires mettant en danger la réserve de flottabilité du sous-marin, il a été décidé de faire appel au support de la société américaine General Electric Boat. En 2016, la Critical Design Review (CDR) a été adoptée et la construction des sous-marins a commencé avec de nouvelles modifications qui affectent le déplacement total du sous-marin et donc sa longueur.
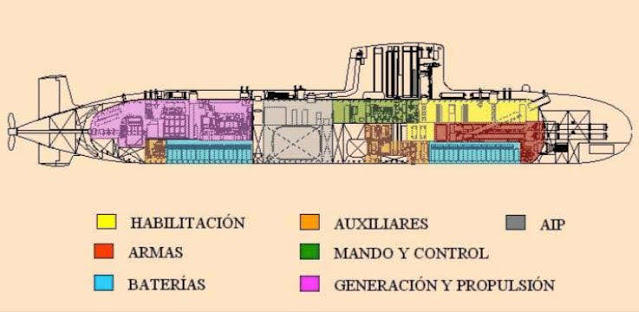
Caractéristiques techniques
Les caractéristiques initiales ont été modifiées, comme cela a été dit, en raison de divers problèmes dans la conception initiale. Après avoir résolu ces erreurs, les principales caractéristiques du sous-marin deviennent:
Longueur 80,81 mètres
Largeur 7,30 mètres
Déplacement 3446 tonnes (immersion) 3220 tonnes (surface)
Equipage 32 + 8
Autonomie 50 jours (15 jours AIP)
Tubes lance-torpilles 6
Générateurs de 3500 Kw 3 MTU Hélice
AIP 1200Kw
Batteries 320 Kw 2 groupes (180 éléments)
Réduction du coefficient d’indiscrétion
Le coefficient d’indiscrétion (ci-après CI), appliqué uniquement aux sous-marins conventionnels, est défini pour une certaine vitesse moyenne, le coefficient entre le temps passé par le sous-marin à charger les batteries et le temps total de navigation aux électriques et au schnorchel.
Avant l’émergence de ce nouveau concept, il n’y avait aucun doute quant à l’importance du CI quelle que soit la mission assignée au sous-marin. Néanamoins, malgré les multiples avantages qu’un sous-marin conventionnel peut offrir par rapport à un sous-marin nucléaire en fonction de la mission à réaliser, le CI reste primordial quand la caractéristique fondamentale d’un sous-marin est la discrétion. Dès lors, de longues périodes au schnorchel augmentent le CI et mettent donc cette discrétion en péril, jusqu’à faire échouer la mission et même perdre l’initiative si nécessaire dans le combat naval conventionnel.
Avantages et inconvénients d’un sous-marin diesel
Comme on l’a déjà dit, selon le type de mission à réaliser, chaque type de sous-marin présente des caractéristiques qui le rendent idéal pour un type de mission.
Il faut distinguer fondamentalement deux groupes principaux selon le type de propulsion utilisé. Le sous-marin conventionnel, qui utilise des générateurs diesel pour charger les batteries grâce à la procédure de plongée en apnée, lorsqu’il est immergé et à induction en surface lorsqu’il navigue en surface. Le deuxième groupe principal est constitué des sous-marins nucléaires, qui utilisent un réacteur nucléaire qui alimente une turbine à vapeur fournissant une énergie électrique illimitée pour propulser le sous-marin.
Le sous-marin conventionnel présente les caractéristiques suivantes par rapport au sous-marin nucléaire:
- Il peut se poser sur le fond, car la réfrigération des sous-marins nucléaires est en partie basse et ils ne peuvent donc pas effectuer ce type de manœuvre.
- Il est plus discret que le sous-marin nucléaire, puisque le réacteur lui-même et ses systèmes de refroidissement génèrent plus de bruit à basse vitesse qu’un sous-marin classique.[NDLR: infondé avec un réacteur à circulation naturelle]
- Il est plus petit et donc plus manœuvrant par faibles fonds, ce qui permet de mener des opérations de renseignement avec plus d’agilité et de sécurité.
Au contraire, ses inconvénients fondamentaux sont:
– La fatigue de l’équipage, car l’espace disponible est bien moindre que dans un sous-marin nucléaire et les conditions de vie à bord sont beaucoup plus dures. Avec tout cela, la fatigue affecte la concentration des équipages, provoquant une démotivation et même des erreurs par manque de motivation.
– La capacité des batteries pose problème car le sous-marin est toujours limité par celle-ci dont la charge dépend de la situation tactique .
– Contrairement aux sous-marins nucléaires, l’air n’est pas renouvelé. Dès lors :
- Il y a épuisement de l’O2, par respiration et combustion,
- Le dioxyde de carbone augmente à cause de la respiration humaine, de l’utilisation de la cuisine et de la vie quotidienne comme l’ouverture d’une canette de soda,
- Le monoxyde de carbone s’accumule par combustion incomplète des gaz d’échappement du moteur, qui sont rejetés dans le sous-marin, augmentation de la vapeur d’eau due à la respiration, à l’évaporation des cales et à la cuisson,
- Il peut également y avoir présence de gaz ( fréon) et de polluants issus de réservoirs sanitaires, des peintures, des solvants,
- Dans le cas de la charge de la batterie, le H2 peut augmenter et dans le pire des cas, si l’eau salée est mélangée à l’électrolyte des batteries H2SO4, du Cl peut se former, ce qui serait dangereux sinon mortel pour l’équipage à des concentrations même faibles.
– Sa vitesse maximale est de 20 nœuds pour les 40 nœuds atteints par le nucléaire, bien qu’il soit vrai que lorsqu’un sous-marin navigue à ces vitesses, il est pratiquement aveugle et excessivement indiscret, devant s’arrêter ou redescendre à des vitesses sous-marines conventionnelles pour pouvoir écouter ce qui l’entoure. Au contraire, atteindre des vitesses aussi élevées leur permet même d’échapper à certaines torpilles des années 90 et même de la première décennie du 21e siècle, mais pas à la dernière génération comme la torpille DM2A42 dont la vitesse, pour son modèle le plus avancé, atteint 45 nœuds et il lui est évidemment impossible d’échapper à la torpille russe Shkval.
– Son CI est toujours supérieur à celui du sous-marin nucléaire, lequel est nul, car il doit recharger ses batteries en fonction de la décharge qu’il a subie au cours de sa mission et, également, renouveler l’air vicié à l’intérieur du sous-marin.
CHAPITRE 1
1.1. Différents systèmes AIP
Depuis quelques années maintenant, les sous-marins à propulsion AIP, également appelés sous-marins anaérobies, ont commencé à apparaître sur les listes de navires de différentes marines, comprenant par anaérobie tout ce qui peut vivre ou fonctionner sans la présence d’oxygène atmosphérique. Bien que la référence pour ce type de technologie soit les navires à propulsion nucléaire, ce n’est pas une solution intéressante sauf pour les grandes marines, pour des raisons politiques et sociales, de coût ou de complexité technique. C’est principalement pour cette raison que d’autres solutions ont été recherchées pour réaliser un système indépendant de l’air, et bien qu’au sens strict du terme, dans un sous-marin nucléaire, sa centrale fonctionne sans avoir besoin d’oxygène de l’air.
Ces nouvelles alternatives ont été développées principalement en Allemagne, en Suède et en France, répondant aux exigences essentielles d’autonomie pour l’accomplissement de missions dans lesquelles le facteur de discrétion joue un rôle fondamental. D’une manière générale, la propulsion anaérobie peut être définie comme un ensemble d’éléments qui transforment l’énergie chimique ou thermique que le système lui-même stocke, en énergie mécanique ou électrique, sans être en contact avec l’atmosphère. Ces dernières années, ils ont connu un développement spectaculaire. Leur capacité actuelle et leurs perspectives d’avenir en font un complément fondamental à la propulsion conventionnelle.
1.2. Les précurseurs des systèmes AIP
1.2.1. Walter Turbine: À la fin de la Seconde Guerre mondiale, l’ingénieur allemand Hellmuth Walter a conçu le premier sous-marin avec la technologie AIP, visant à obtenir de longues périodes d’immersion et des vitesses élevées pour gagner un avantage dans ses confrontations avec les Alliés. Ils étaient alimentés par une turbine qui utilisait du peroxyde d’hydrogène à 90% de pureté comme combustible / comburant.
Le peroxyde d’hydrogène passait dans une chambre où, au contact d’un catalyseur, il se décomposait en eau et en oxygène. Lors du passage de ces éléments dans une seconde chambre, appelée combustion, un carburant organique y a été injecté, provoquant une oxydation / combustion. À la suite de cette réaction, de la vapeur d’eau et du dioxyde de carbone ont été générés à une température et une pression élevées. Ce gaz était dirigé vers une turbine qui faisait fonctionner un arbre et son hélice fixée à son extrémité tournait. Une partie de cette vapeur a été récupérée sous forme d’eau lors du passage dans un condenseur, le dioxyde de carbone a été dissous dans l’eau salée et expulsé vers la mer, et la vapeur a été redirigée vers la chambre de combustion, pour produire plus de vapeur dans la réaction de la peroxyde avec le catalyseur et le carburant.
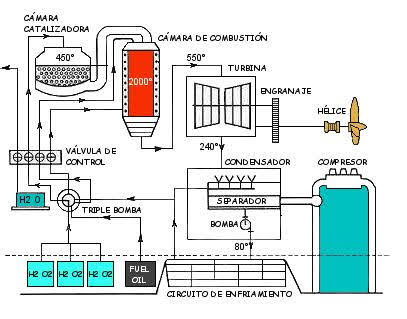
En raison de l’instabilité du peroxyde d’hydrogène, ce système a été mis au rebut, car avec une fuite minimale, des incendies peuvent survenir car il réagit facilement avec la graisse, le caoutchouc, les toiles de peinture … De plus, la consommation était très mile, le sous-marin avait besoin de 25 fois plus de carburant que son moteur diesel équivalent. Malgré tout, les sous-marins dotés de cette propulsion ont atteint 25 nœuds en immersion.
1.2.2. Diesel en circuit fermé (CCD):Dans les années 1990, la marine allemande a développé un système basé sur un moteur diesel à cycle fermé, qui fonctionnait en conjonction avec deux autres moteurs diesel conventionnels. L’énergie électrique était générée par un alternateur couplé au moteur diesel modifié. Dans ce système, les gaz d’échappement étaient partiellement recirculés vers l’admission. Ces gaz, constitués principalement de CO2, d’argon et de vapeur d’eau, laissent le moteur à haute pression et température. Ils sont introduits dans un absorbeur, où le dioxyde de carbone se dissout dans l’eau de mer et est expulsé dans la mer sans formation de bulles. De là vient un flux de gaz auquel s’ajoutent de l’oxygène et de l’argon (gaz inerte qui ne réagit pas lors de la combustion) pour augmenter le coefficient adiabatique des gaz d’admission,
C’est un système très sûr car il n’y a pas de substances toxiques ou explosives, et le même carburant est utilisé que pour les moteurs diesel principaux, donc un réservoir spécifique pour le diesel modifié à cycle fermé ne serait pas nécessaire. Mais il présente aussi des inconvénients tels que la faible performance du système (environ 30%), l’élimination du CO2 consomme une partie de l’énergie produite et ses équipements occupent un espace important, et, le plus critique quand on parle de sous-marins, c’est qu’être un Le moteur à combustion interne sera bruyant en raison des explosions des cylindres et produira également des vibrations, bien que l’on essaie d’éviter celles-ci par l’encapsulation et l’isolation de la structure.
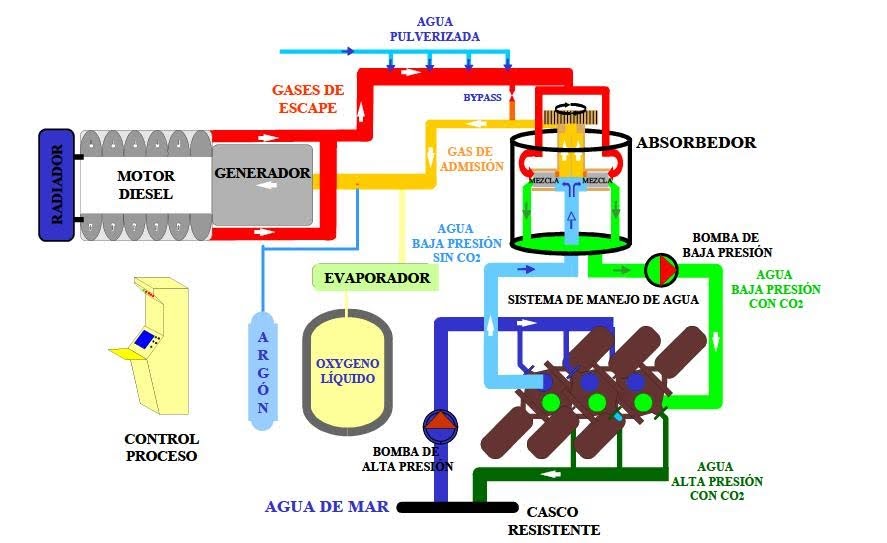
1.3. Systèmes actuellement disponibles
Il existe actuellement cinq types de propulsion AIP, opérationnels ou en construction dans les sous-marins. Il
s’agit du moteur Stirling (Kockums), du système MESMA (DNCS), des
réservoirs cryogéniques contenant de l’hydrogène (Rubin), des systèmes
basés sur l’obtention d’hydrogène à partir d’hydrures métalliques (HDW /
Siemens) et du système par reformage du bioéthanol (Navantia /
Hynergreen).
1.3.1. Moteur Stirling: Datant du début des années 1990, c’est le premier des systèmes anaérobies en opération. Bien
que le moteur Stirling ait été théoriquement défini au 19ème siècle par
le révérend écossais Robert Stirling, la technologie actuelle a été
développée par la société suédoise Kockums. Le
moteur de Stiling effectue les mêmes processus de chauffage et de
refroidissement d’un gaz dans une machine à vapeur, mais tout se passe à
l’intérieur du moteur et le gaz est de l’air au lieu de la vapeur
d’eau, la chaudière n’est donc pas nécessaire. Le
principe de fonctionnement est uniquement le chauffage et le
refroidissement, à volume constant, d’un fluide de travail, qui peut
être de l’air, de l’hélium, de l’hydrogène et même un liquide, grâce à
l’apport de la chaleur générée dans une chambre de combustion externe.
Le
diesel passe dans la chambre de combustion avec l’oxygène cryogénique
(préalablement évaporé), transférant la chaleur générée par un échangeur
vers une zone déterminée d’un circuit de gaz fermé (point chaud). Il
se compose de deux cylindres et de deux pistons, l’un d’eux
fonctionnant devant une source chaude (chambre de combustion) et l’autre
devant une source froide. Le gaz entre les deux pistons (Hélium) se déplace en continu du foyer chaud au foyer froid. Ce gaz chauffé est chauffé dans un cylindre et se dilate, amenant le piston à se déplacer vers le point mort bas. C’est à ce stade que le travail est généré. De
là, le piston se déplace vers le point mort haut et le gaz passe à
travers le régénérateur, absorbant une partie de l’énergie thermique, ce
qui refroidit le gaz et diminue sa pression. Le piston du cylindre de mise au point à froid descend au point mort bas. Le
piston froid se déplace alors dans une course ascendante, comprimant le
gaz et le chauffant, et, lors de son retour dans la chambre chaude, il
augmente sa température lors de son passage dans le régénérateur. Tout ceci provoque un mouvement alternatif des pistons qui est transmis à un vilebrequin au moyen de bielles. En
bref, c’est une machine qui délivre du travail à la suite de
l’expansion et de la contraction d’un gaz en deux phases isothermes et
deux phases à volume constant. Tout ceci provoque un mouvement alternatif des pistons qui est transmis à un vilebrequin au moyen de bielles. En
bref, c’est une machine qui délivre du travail à la suite de
l’expansion et de la contraction d’un gaz en deux phases isothermes et
deux phases à volume constant. Tout ceci provoque un mouvement alternatif des pistons qui est transmis à un vilebrequin au moyen de bielles. En
bref, c’est une machine qui délivre du travail à la suite de
l’expansion et de la contraction d’un gaz en deux phases isothermes et
deux phases à volume constant.
Certains
avantages de ce système sont qu’il a de meilleures performances qu’un
moteur à combustion interne (35%) ainsi qu’un fonctionnement silencieux
avec de faibles vibrations en raison du peu de pièces mobiles dont il
dispose et que la combustion est continue, pas avec des explosions
périodiques. Comme inconvénients, nous avons l’élimination du CO2, qui limite la hauteur maximale à 200 mètres. L’étanchéité du moteur est essentielle, car le gaz de travail doit rester complètement étanche.
Actuellement, il existe des sous-marins opérationnels avec ce système AIP dans plusieurs pays:
- La Suède , avec ses 3 sous-marins de classe «Gotland» (initialement construits avec le système Stirling) et 2 sous-marins de classe «Sódermanland» (anciennement classe «Vástergótland», reconvertie en Stirling après un travail de demi-vie effectué par Kockums).
- Singapour , deux sous-marins de classe «Archer» (ancienne classe «Vástergótland» achetée à la Suède).
- Japon , dix sous-marins de classe «Sóryüs» et quatre autres en construction, les cinq premiers de Mitsubishi Heavy Industries et les cinq suivants de Kawasaki Heavy Industries avec une licence de construction de la société suédoise Korckums Naval Solutions.
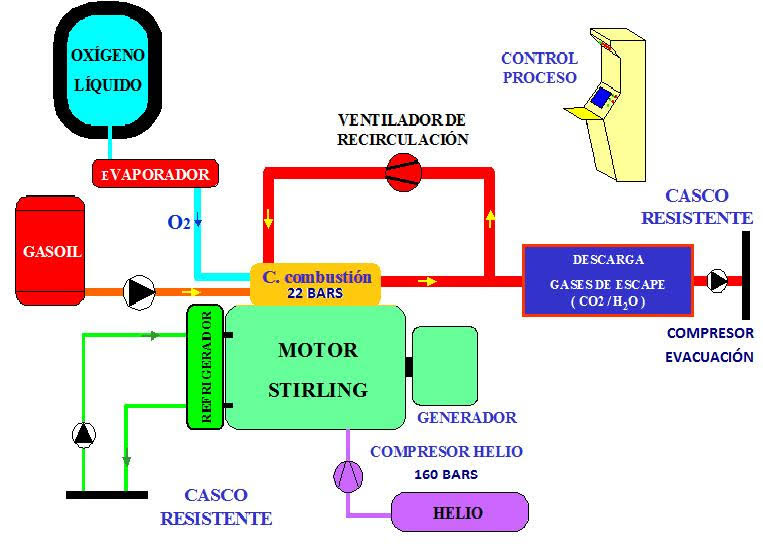
1.3.2. Module d’énergie sous-marine autonome (MESMA, Module de’Energie Sous-Marine Autonome): L’AIP appelé MESMA consiste en un module d’une turbine à vapeur conventionnelle, où l’énergie thermique est convertie en énergie électrique à l’aide d’un cycle de Rankine conventionnel, qui Il comprend un générateur de vapeur, des turbo-alternateurs et un condenseur.
La vapeur est chauffée par un circuit primaire dans une chambre de combustion, brûlant un mélange gazeux d’éthanol et d’oxygène. L’oxygène est stocké sous pression cryogénique, à -185 °, à partir de là, il est pompé dans un vaporisateur pour le convertir en gaz. Il est ensuite envoyé dans une chambre de combustion où, combiné à l’éthanol, une puissance thermique de 700 ° C est produite à une pression de 60 bars. Un recirculateur recycle la partie des gaz d’échappement refroidis pour réguler la température à l’intérieur du circuit primaire. Ces gaz traversent un échangeur de chaleur. Les gaz de combustion sont expulsés directement dans la mer sans qu’il soit nécessaire d’utiliser un système de gestion de l’eau pour la pré-dissolution et indépendamment du niveau de fonctionnement grâce à la pression de service élevée de la chambre de combustion.
Le circuit de vapeur secondaire est celui chargé de déplacer la turbine avec laquelle, grâce à un alternateur relié mécaniquement, de l’énergie électrique est produite pour recharger les batteries. Cette vapeur, après la turbine, passe par un condenseur chauffant un circuit d’eau salée, qui à son tour est responsable de l’augmentation de la température d’un circuit intermédiaire qui est celui qui vaporise l’oxygène liquide, profitant ainsi au maximum de l’énergie.
L’oxygène liquide et l’éthanol doivent être stockés séparément à une distance suffisante pour répondre aux normes de sécurité strictes et aux exigences de stockage dangereux. Ce système peut également fonctionner avec du diesel, étant capable d’utiliser les mêmes réservoirs diesel que les moteurs de la centrale électrique. Les normes de contrôle et de confinement doivent beaucoup à la vaste expérience de DNC dans le domaine de la propulsion nucléaire, entreprise française qui a commencé à développer cette conception au début des années 1980.
L’état de développement de ce système est avancé et il est installé dans un sous-marin de la marine pakistanaise. Il a une grande fiabilité avec un fonctionnement et une maintenance sûrs du point de vue des effectifs. D’autre part, il a un rendement réduit (20%) et nécessiterait de grandes quantités d’oxygène liquide et d’éthanol, ce qui augmenterait la longueur du sous-marin de 8 ou 9 mètres pour les besoins du système.
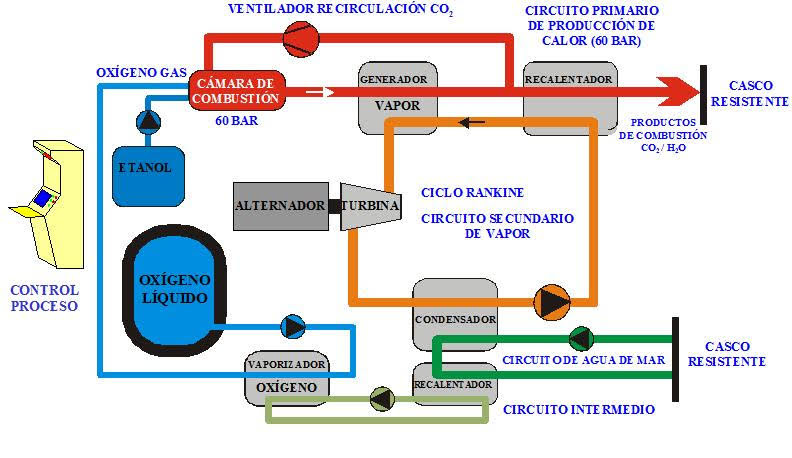
Les trois types suivants d’AIP sont alimentés par des piles à combustible ou des piles, dans lesquelles l’hydrogène et l’oxygène produisent de l’énergie électrique en déplaçant des électrons d’une anode à une cathode, ce qui sera expliqué en détail plus loin. La différence entre les trois est la façon dont l’hydrogène est obtenu pour cette réaction.
1.3.3. Réservoirs d’hydrogène cryogénique (Rubin):Il
s’agit du système AIP utilisé dans les sous-marins de classe LADA
(classe Sankt Petersburg) de la marine russe et est destiné aux dérivés
de cette classe. Il est
conçu par la société Rubin Design Bureau, basé sur l’existence de
réservoirs cryogéniques internes verticaux et horizontaux contenant
respectivement de l’oxygène et de l’hydrogène. L’inconvénient de ce système est le grand danger de stocker une grande quantité d’hydrogène. Toute fuite produirait une réaction exothermique incontrôlable. De
plus, l’hydrogène doit être stocké à des températures proches de -250 °
C, inférieures à son point d’ébullition normal à 1 atm qui est de
-252,76 ° C (20,38 ° K). Il
est introduit dans une cuve à double paroi isolée thermiquement, de
manière à minimiser les pertes par évaporation, qui peuvent atteindre 1 à
2% par jour.
De
manière générale, il s’agit d’un système qui utilise des piles à
combustible LOX-H2, de l’hydrogène et de l’oxygène liquide, pour la
conversion directe de l’énergie chimique d’un combustible en énergie
électrique et en chaleur. Après
des essais en mer effectués sur les sous-marins avec ce système, et
après quelques améliorations après la paralysie du projet pendant
plusieurs années, il y a 3 sous-marins en service et un quatrième prévu
pour 2019. Par ailleurs, la Russie a l’intention d’augmenter son marché
d’exportation en vendant une variante du prototype (Projet 950 AMUR),
moins cher que le projet germano-italien (212) et franco-espagnol
(Scorpène).
1.3.4. Obtention d’hydrogène à partir d’hydrures métalliques (HDW / SIEMENS): L’hydrogène est un élément très abondant, mais pas à l’état pur, mais on le trouve en combinaison avec d’autres éléments. Il peut être obtenu à partir d’eau, d’hydrures ou d’hydrures métalliques. Le stockage de H2 à l’état pur présente de nombreuses difficultés, comme cela a déjà été vu précédemment dans cette monographie, en raison de sa faible température de liquéfaction et du fait qu’il réagit violemment au contact de l’oxygène, toujours avec une réaction exothermique incontrôlable. La meilleure procédure mise en œuvre aujourd’hui dans les sous-marins est celle des hydrures métalliques, car elle est la plus sûre et la plus fiable, mais elle est aussi la plus coûteuse.
La base de cette méthode est que certains métaux et alliages métalliques ont la propriété de former des liaisons covalentes réversibles lorsqu’ils réagissent avec l’hydrogène, formant ce que l’on appelle des hydrures métalliques, qui se décomposent lorsqu’ils sont chauffés en libérant de l’hydrogène. L’hydrure est formé en soumettant un certain métal à une pression d’hydrogène élevée, ce qui amène le métal à piéger des atomes d’hydrogène dans sa structure cristalline comme une éponge. Il suffit alors de réduire la pression externe pour que le métal libère l’hydrogène. Les hydrures ont la propriété importante de pouvoir être utilisés pour stocker l’hydrogène pendant de nombreux cycles d’association-dissociation sans diminuer leur capacité de stockage. Réservoirs d’hydrure métallique donc ils ont à l’intérieur un alliage capable d’absorber l’hydrogène qui est ensuite récupéré en apportant de la chaleur. Les hydrures métalliques portent une proportion de 1 à 7% en poids d’hydrogène. Dans les métaux tels que le titane, la concentration d’énergie par unité de volume est plus élevée que dans l’hydrogène liquide. Plus de 200 alliages différents ont été étudiés, les plus adaptés étant ceux du groupe V des métaux de transition, tant pour leur capacité de stockage que pour leur prix, leur non-décrépitation et la basse température nécessaire pour dissocier l’hydrure.
Les réservoirs d’hydrure métallique présentent deux inconvénients: l’un est que l’apport d’énergie est nécessaire pour récupérer l’hydrogène, et le second est que tout l’hydrogène qui est introduit dans les métaux n’est pas récupérable, ses performances ne sont pas à 100%.
Actuellement, de nombreux sous-marins sont opérationnels ou en construction, pouvant nommer le type 212A 4 U-31 d’Allemagne et d’Italie, le type 212 A Batch 2 d’Allemagne, le type 214 de Grèce, Corée du Sud, Turquie et Pakistan, la classe Dolphin d’Israël et tapez 209/1400 depuis le Portugal.
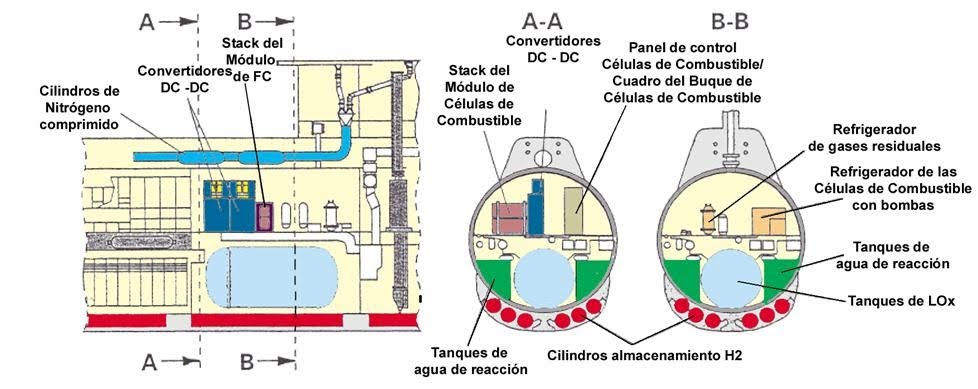
1.3.5. Obtenir de l’hydrogène par reformage du bioéthanol (NAVANTIA / Hynergreen): Comme les deux systèmes précédents, dans celui-ci l’objectif est de charger des piles à combustible, mais cette fois grâce à l’utilisation de bioéthanol produit à partir de la biomasse. Avec cette nouvelle méthode, les performances thermodynamiques sont considérablement augmentées et les polluants gazeux produits lors de la combustion sont éliminés.
Pour obtenir de l’énergie, il faut prendre en compte deux phases: la première d’obtention d’hydrogène en ajoutant du bioéthanol et de l’eau / oxygène sur un catalyseur; et deuxièmement, avec l’hydrogène obtenu et l’oxygène fourni, l’énergie nécessaire pour les batteries serait obtenue. En tant que sous-produits, le CO2 est obtenu à partir de la réaction de reformage et l’eau de la pile à combustible.
Le processus lui-même d’obtention d’hydrogène sera expliqué en détail plus loin. Après ce reformage dans le système de traitement du bioéthanol (SPB), on obtient un mélange gazeux contenant du dioxyde de carbone et de l’hydrogène. Après cette réaction, l’hydrogène est fourni à la pile à combustible pour obtenir de l’énergie, et le dioxyde de carbone sera éliminé après avoir été dissous dans l’eau de mer à pression constante, ce qui permet de rendre le fonctionnement de l’installation AIP indépendant de l’élévation de exploitation du navire.
Comme avantages de ce système, on peut souligner les bonnes performances, qui sont d’environ 25,5% (les performances théoriques des piles à combustible après obtention d’hydrogène sont de 95%, mais en pratique elles sont de 70-75% ). Il a également un faible impact sur l’environnement, car il n’y a pas de processus de combustion et qu’il n’y a pas de formation d’azote ou de soufre, bien que le dioxyde de carbone se forme dans une proportion beaucoup plus faible que lors de la combustion. Non seulement cela, mais le bioéthanol est une source d’énergie renouvelable, obtenue par fermentation de sucres, de céréales ou de biomasse, et ne contient pas d’impuretés nocives pour le reformeur et les cellules, comme le soufre. Sa signature acoustique et thermique est faible et sa technologie est en constante évolution, avec des perspectives prometteuses.
Comme inconvénients, nous pouvons souligner que le stockage et la distribution d’hydrogène présentent un risque pour la sécurité du personnel et du sous-marin lui-même, en particulier dans les zones de passage de l’hydrogène pur. On peut aussi signaler qu’il y a production de CO2, qui bien que ce soit un problème résolu, suppose une réserve d’espace à l’intérieur du navire pour son élimination.
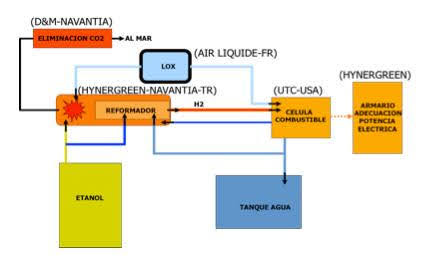
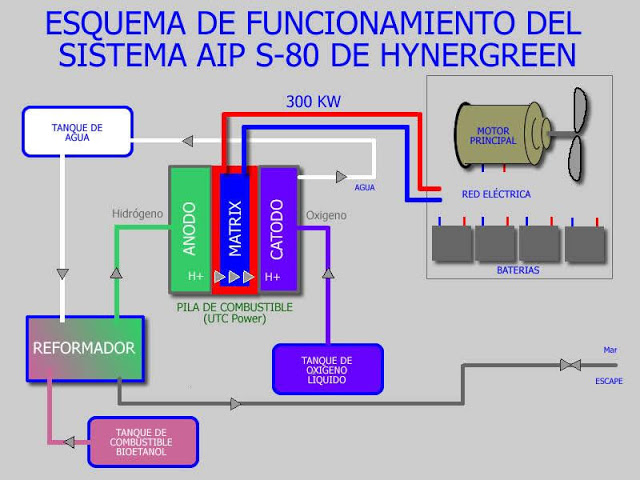
CHAPITRE 2
2.1. Fonctionnement du S-80 AIP
Comme
expliqué précédemment, le futur sous-marin S-80 utilisera un système de
propulsion indépendante de l’air avec l’obtention d’hydrogène à partir
du reformage du bioéthanol. Cependant,
il est pratique d’expliquer ce que sont le processeur au bioéthanol
(SPB) et une pile à combustible et comment ils fonctionnent.
Le principal objectif du système de traitement du bioéthanol (2) est de transformer un flux de bioéthanol en hydrogène adapté pour alimenter la pile à combustible. Pour
cela, il dispose d’une chambre de combustion, où la chaleur nécessaire
au développement de la réaction endothermique initiale est fournie, et
de deux modules: le reformeur, où a lieu la transformation du bioéthanol
en hydrogène, et le système de purification des gaz. résidus.
Il existe actuellement trois types de réformateurs de base:
- Ceux d’oxydation partielle, dans lesquels un mélange d’oxygène pauvre est mis à réagir avec le carburant, normalement utilisés avec des hydrocarbures lourds tels que le diesel, l’essence ou le pétrole lourd.
- Autothermique, dans lequel le carburant, la vapeur et l’oxygène sont amenés ensemble à un catalyseur.
- Reformeurs à vapeur. Ce sont les plus efficaces et les plus économiques, et c’est celui que le S-80 utilisera. Le reformage à la vapeur est basé sur le principe que la teneur en hydrogène du carburant se décompose en présence de vapeur excédentaire dans les catalyseurs au nickel pour produire le mélange hydrogène / monoxyde de carbone. La formule de réaction est la suivante:
CnHm + nH2O + chaleur -> nCO + (n + m / 2) H2
Un grand avantage de ce dernier type de reformeur est que l’hydrogène présent dans l’eau sera libéré au cours de la réaction, contribuant ainsi à la production totale d’hydrogène. De plus, étant un procédé endothermique, une grande partie de l’énergie peut être récupérée et réintroduite dans le procédé, améliorant ainsi l’efficacité thermique du reformeur.
Après le reformeur, il est nécessaire de disposer d’un système d’élimination du monoxyde de carbone, car il empoisonne les catalyseurs et les membranes polymères des piles à combustible. Le processus se poursuit avec le système de purification au moyen de la réaction «Water Gas Shift» (Water Gas Shift [3]). Il s’agit d’une réaction exothermique réalisée dans une étape à haute température (350 ° C) et une autre étape à basse température (200 ° C) [4] avec refroidissement intermédiaire. De cette manière, on obtient une diminution de la concentration en monoxyde de carbone et une augmentation de la quantité d’hydrogène, selon la formule suivante:
CO + H2O -> H2 + CO2
A l’issue de cette étape, une purification est réalisée à l’aide de la « Réaction d’Oxydation Sélective » (COPROX), qui est une autre réaction exothermique, cette fois à 150 ° C, diminuant la concentration en CO de l’ordre de 20 ppm, de sorte que les batteries leur efficacité n’est pas affectée de manière significative. Cette purification se fait selon la formule:
CO + I / 2O2 -> CO2
Les deux réactions qui ont lieu dans le purificateur étant exothermiques, et que la température de l’hydrogène à l’entrée de la pile à combustible ne peut dépasser 40 ° C, il faut d’abord le forcer à traverser un échangeur de chaleur. Grâce à ce système, la chaleur des réactions de purification est utilisée pour le chauffage et l’évaporation des réactifs et la réaction de reformage.
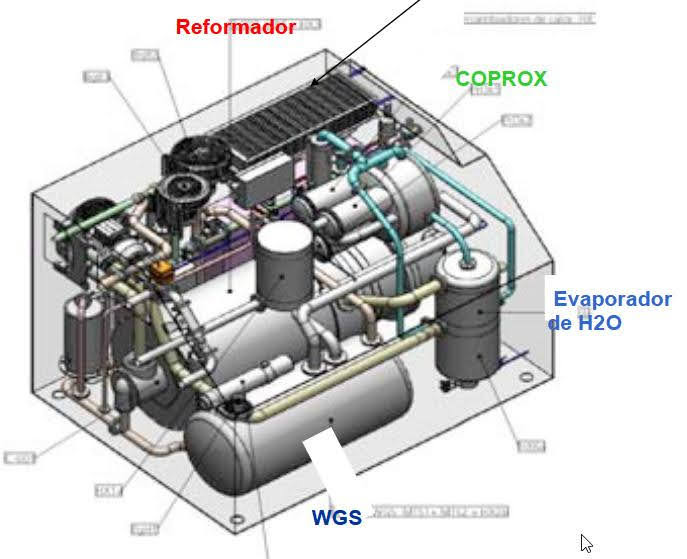
Les
piles à combustible sont des dispositifs électrochimiques pour la
conversion directe de l’énergie chimique d’un combustible en énergie
électrique et en chaleur, dans un processus inverse à l’électrolyse de
l’eau. Ils sont constitués
d’un ensemble de cellules électrochimiques, dont chacune est constituée
de deux électrodes séparées par une matrice contenant l’électrolyte. Le
combustible est l’hydrogène et l’oxygène oxydant, obtenant comme seuls
produits de réaction l’eau, l’énergie électrique et la chaleur.
Actuellement, il existe de nombreux types ou familles de piles à combustible classés selon leur électrolyte:
- Alcaline (PCA / AFC)
- Batteries à l’acide phosphorique (PCAF / PAFC)
- Piles d’oxyde solide (PCOS / SOFC)
- Cellules polymères ou membranaires (PCPS / PEMFC)
- Empilements de carbonates fondus (PCCF / MCFC).
Dans
le système qui sera intégré dans le S-80, on utilisera des PEM (Polymer
Electrolyte Membrane ou Proton Exchange Membrane), dont l’électrolyte
est un polymère organique solide sous forme de membrane. Ce
sont ceux qui présentent les plus grands avantages pour une utilisation
dans des installations où le poids et le volume sont déterminants,
comme c’est le cas pour les sous-marins. Ils
constituent le noyau essentiel du système de propulsion car à
l’intérieur, c’est là que l’énergie chimique des réactifs est
transformée en énergie électrique. Certains des avantages de ce type de batterie sont les suivants:
- Taille et poids réduits.
- La puissance fournie est facilement adaptable à la demande.
- Longue durée de vie (environ 20 000 heures).
- Faible température de fonctionnement, ce qui entraîne moins de corrosion, un démarrage rapide et une minimisation des pertes dues au transfert de chaleur vers l’extérieur.
- Signature acoustique négligeable et signature thermique négligeable (60-80 ° C)
Comme mentionné précédemment, l’énergie chimique est convertie en énergie électrique dans ces batteries, obtenant de l’eau distillée comme produit résultant. Alors que dans l’électrolyse, il est bien connu, le processus inverse est moins bien connu, et on obtient que l’énergie libérée n’est pas dissipée mais est convertie en énergie électrique, ce qui est obtenu en empêchant les gaz de réaction (H2 et O2) contacter directement. Cette séparation est réalisée grâce à la membrane, l’électrolyte, qui ne laisse passer qu’un seul d’entre eux et uniquement ioniquement. Dans ce cas, étant un polymère fluorocarboné, en plus d’être un isolant électronique, c’est un excellent conducteur d’ions hydrogène, donc les ions qui le traversent sont H +.
L’hydrogène gazeux sous pression pénètre dans l’anode, où un catalyseur au platine décompose la paire de molécules en quatre cations H + et quatre électrons libres. La membrane polymère est «imperméable» aux électrons, mais permet aux cations hydrogène de traverser la cellule jusqu’à la cathode, où ils se combinent avec l’oxygène pour former de l’eau. Les électrons quittent l’anode pour entrer dans le circuit interne sous forme de courant électrique. Pendant ce temps, à la cathode, chaque molécule d’oxygène est dissociée catalytiquement en ses atomes composants. Le principal avantage du concept de «pile à combustible» est que le seul produit d’échappement, comme déjà mentionné, est de l’eau pure, qui maintient la membrane hydratée et est expulsée avec l’excès de gaz.
Bien que théoriquement 1’23V doive être produit, en pratique 0,7V est généré dans chaque cellule. Le S-80 transportera deux piles composées de 216 cellules regroupées en six paquets ou piles.
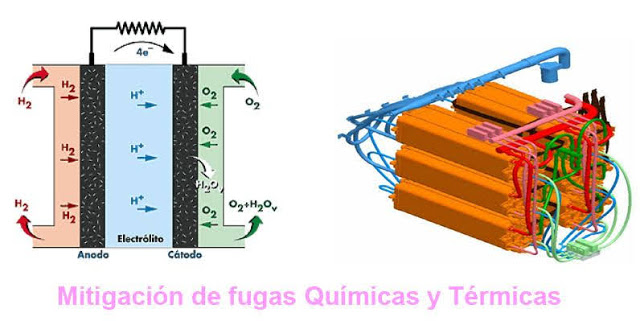
À
ce stade de l’explication du fonctionnement du système, nous constatons
que le bioéthanol a déjà été traité et nous avons obtenu l’hydrogène,
et après l’avoir purifié par deux processus différents, nous avons
alimenté les piles à combustible, produisant l’énergie électrique
nécessaire à la charge. batteries et fourniture au navire. La
seule chose qui reste à ce moment est l’élimination du CO2 que nous
avons obtenu après le système de purification des gaz indésirables.
Pour
son élimination, il est nécessaire de dissoudre les bulles de dioxyde
de carbone dans l’eau de mer, puis d’expulser cette solution vers
l’extérieur avec les niveaux de discrétion typiques d’un sous-marin. Ce
système est le SECO2 6, conçu par Bionet, le CO2 est comprimé et
refroidi, pour plus tard, au moyen de l’éjecteur et du mélangeur du
système, le mélanger et le dissoudre avec l’eau de mer, l’expulsant à
l’extérieur. Le procédé est favorisé par des pressions élevées et des températures basses.
Enfin,
il convient de noter que le stockage de tous les produits nécessaires
au fonctionnement du système est franchement important, et chacun d’eux
nécessite des mesures particulières pour la sécurité du sous-marin.
L’oxygène
liquide (-185 ° C) est stocké dans une cuve de type «Dewars» (double
paroi) d’environ 7 mètres de long et 4 mètres de diamètre, d’une
capacité d’environ 60 m3. Il
est composé de deux conteneurs, l’un à l’intérieur et l’autre à
l’extérieur, avec un vide entre eux pour éviter des pertes de
température inutiles. Le
récipient intérieur est soutenu avec le récipient extérieur par quelques
points d’appui, très légers, pour éviter cette éventuelle vaporisation
de liquide. L’oxygène est
un gaz oxydant, il ne se brûle pas, mais il est dangereux car il fait en
sorte que les matériaux incombustibles le deviennent, et ceux qui
étaient déjà combustibles, brûlent violemment. Les
utilisations de l’oxygène, en résumé, sont les suivantes: alimentation
en oxygène pour la chambre de combustion du reformeur au bioéthanol,
alimentation pour l’élimination du monoxyde de carbone (COPROX), alimentation pour la pile à combustible et alimentation pour la régénération de l’atmosphère. Avant l’utilisation de l’oxygène, il est pompé dans un échangeur de chaleur avec de l’eau glycolée5 , similaire à celui utilisé dans les centrales nucléaires.
Le
bioéthanol est stocké à l’intérieur de la coque résistante, dans trois
réservoirs situés dans la chambre AIP et dans les auxiliaires de proue. La
capacité totale de stockage est de 30 m3, ce qui donne théoriquement au
sous-marin une autonomie de 15 jours en immersion à une vitesse de 4
nœuds.
CHAPITRE 3
Au
cours du chapitre précédent, il a été expliqué de manière claire et
relativement concise comment le système AIP fonctionne et en quoi
consiste ce processus. Mais
il faut vraiment être conscient du véritable saut que ce système
suppose vis-à-vis des sous-marins diesel conventionnels ou même avec
d’autres systèmes AIP et bien sûr, dans sa portée, vis-à-vis des
sous-marins à propulsion nucléaire.
3.1. État de développement et de mise en œuvre du système.
Lors
de la première phase de développement et de conception du projet, en
2003, il a été décidé de confier le développement de la technologie AIP à
la société nationale ABENGOA en raison de sa solvabilité financière et
de son expérience dans les énergies renouvelables. Au
cours de cette première phase, ABENGOA développe un prototype de 10Kw
pour vérifier la viabilité et le développement ultérieur du projet. Après
avoir terminé avec succès cette première phase, une seconde est
développée, dans laquelle ils doivent construire un AIP capable de
générer 300Kw, ce qui leur permettrait de passer les 15 jours sans
plongée en apnée requis par la Marine. Ces dernières années, cette pile à combustible de 300 kW a été fabriquée sur terre et avec une taille considérable. Le problème se pose quand il doit être navalisé. ABENGOA est incapable de construire l’usine de la bonne taille pour tenir dans un sous-marin, pour produire cette même puissance, le projet a donc continué à être retardé. En
2014, face à l’impossibilité de miniaturiser la pile à combustible
selon les spécifications du contrat, la Marine a décidé d’élargir le
champ des possibles développeurs de projets et de pouvoir apporter des
solutions viables pour sa mise en œuvre dans le sous-marin. Après
plusieurs tentatives de diverses entreprises de la région, seuls
ABENGOA, qui a absorbé Hynergreen, et Técnicas Reunidas restent les
principaux véritables développeurs du projet. La
Marine décide d’élargir le champ des possibles développeurs du projet
et qui peuvent apporter des solutions viables pour sa mise en œuvre dans
le sous-marin. Après
plusieurs tentatives de diverses entreprises de la région, seuls
ABENGOA, qui a absorbé Hynergreen, et Técnicas Reunidas restent les
principaux véritables développeurs du projet. La
Marine décide d’élargir le champ des possibles développeurs du projet
et qui peuvent apporter des solutions viables pour sa mise en œuvre dans
le sous-marin. Après
plusieurs tentatives de diverses entreprises de la région, seuls
ABENGOA, qui a absorbé Hynergreen, et Técnicas Reunidas restent les
principaux véritables développeurs du projet.7 . En
2017, Técnicas Reunidas a développé et breveté un système AIP qui,
selon elle, peut être intégré au sous-marin et produire l’énergie
nécessaire pour le propulser pendant 15 jours. La
Marine de son côté attend de voir les résultats et ABENGOA continue
d’essayer de développer le système pour remporter le contrat pour lequel
elle a été choisie il y a plus de 15 ans.3.2. Avantages et capacités attendus.
Tout
au long de ces travaux, les caractéristiques du système AIP que la
Marine a exigées de son entrepreneur ont été vues mais, au vu des
retards et des difficultés auxquels ce projet a dû faire face, il est
commode de comparer avec d’autres systèmes existants les avantages qu’il
offrira aux futurs sous-marins S-80 par rapport aux sous-marins
existants et éprouvés.
La
première est évidente, en utilisant un reformeur de bioéthanol, on
évite la dépendance à l’hydrogène et on doit le transporter à bord comme
cela se produit dans les sous-marins allemands de type 212. L’Espagne
est le premier producteur mondial de bioéthanol comme on peut le voir
dans le tableau suivant et avec cela, une dépendance technologique et
matière première est évitée pour alimenter le sous-marin tout au long de
sa vie opérationnelle.

D’autre
part, l’utilisation du bioéthanol comme carburant assure la stabilité,
le transport, la facilité de manutention, le stockage dans des
réservoirs et, bien sûr, la sécurité de l’équipage du sous-marin. De
plus, étant un système créé spécifiquement pour ce projet, l’efficacité
de la batterie est plus élevée pour deux raisons fondamentales. L’hydrogène produit n’a pas besoin d’être pur à 100% et la production d’énergie avec ce reformage est extrêmement élevée.
Si
nous le comparons avec le système AIP le plus utilisé, développé pour
les sous-marins de type 212 par la société allemande HDW en
collaboration avec Siemens, on peut noter que:
- – Le système allemand stocke l’hydrogène au moyen d’hydrures métalliques, qui a un poids très élevé, ce qui limite logiquement la réserve de flottabilité dans le sous-marin et l’espace pour d’autres éléments du sous-marin, comme les systèmes d’armes.
- – Le processus de recharge d’hydrogène doit être réalisé dans des usines spécialisées, avec un personnel technique hautement qualifié et à un coût élevé en raison de la complexité du processus.
- – Les piles à combustible mises au point par la société UTC Power utilisées, associées au reformage du bioéthanol, ont fourni 7% de puissance en plus que celles fabriquées par Siemens.
La
puissance totale que le système doit fournir doit assurer, selon les
spécifications techniques du contrat, un temps minimum de 15 jours à une
vitesse constante de 3-4 nœuds. Selon
les dernières études et tests réalisés, Técnicas Reunidas a proposé son
modèle breveté et testé à la Marine et à la Navantia. Après
plusieurs audits dans lesquels il intègre une feuille de route et un
plan réaliste et viable à temps pour sa future navalisation, le projet a
été approuvé et bénéficie donc du soutien des deux institutions pour se
positionner comme le fournisseur final du système AIP pour futurs
sous-marins S-80.
CONCLUSIONS
S’il
est vrai que l’idée d’un système de propulsion indépendant de l’air se
développe depuis la fin de la Seconde Guerre mondiale, le concept
révolutionnaire de l’utilisation du reformage au bioéthanol a permis au
développement de ce complexe de système de poussée d’évoluer.
Le
bioéthanol, associé à la pile à combustible, fournira à nos sous-marins
l’énergie nécessaire pour rester en immersion continue pendant au moins
15 jours.
Par
conséquent, au vu des travaux actuels, il peut être conclu que le
développement d’un nouveau système AIP par l’industrie espagnole, s’il
parvient enfin à être installé dans les sous-marins de la classe S-80,
ne se traduira pas seulement par une augmentation des capacités. de ces
sous-marins et une réduction de CI sans précédent dans notre marine,
mais aussi une grande réussite de l’ingénierie navale et des industries
espagnoles, démontrant ainsi qu’ils sont à la pointe dans le
développement de leurs propres projets avec la technologie et la
main-d’œuvre nationale .
Selon
le calendrier actuel des événements, la mise en place du système AIP
dans le sous-marin vous procurera des temps de plongée formidables pour
un sous-marin de sa classe et en fonction des données dont nous
disposons
eu
accès, il est plus que probable que ce sera le sous-marin avec le temps
d’immersion le plus long sans avoir besoin d’une charge de batterie
dans le monde. Placer la
Marine, à la pointe des sous-marins conventionnels et par conséquent,
Navantia dans une excellente position pour pouvoir exporter le produit
vers des marines étrangères et ainsi aider l’économie et le prestige de
l’Espagne dans le monde.
source : elsnorkel